Soon reconditioned products in all our equipment?
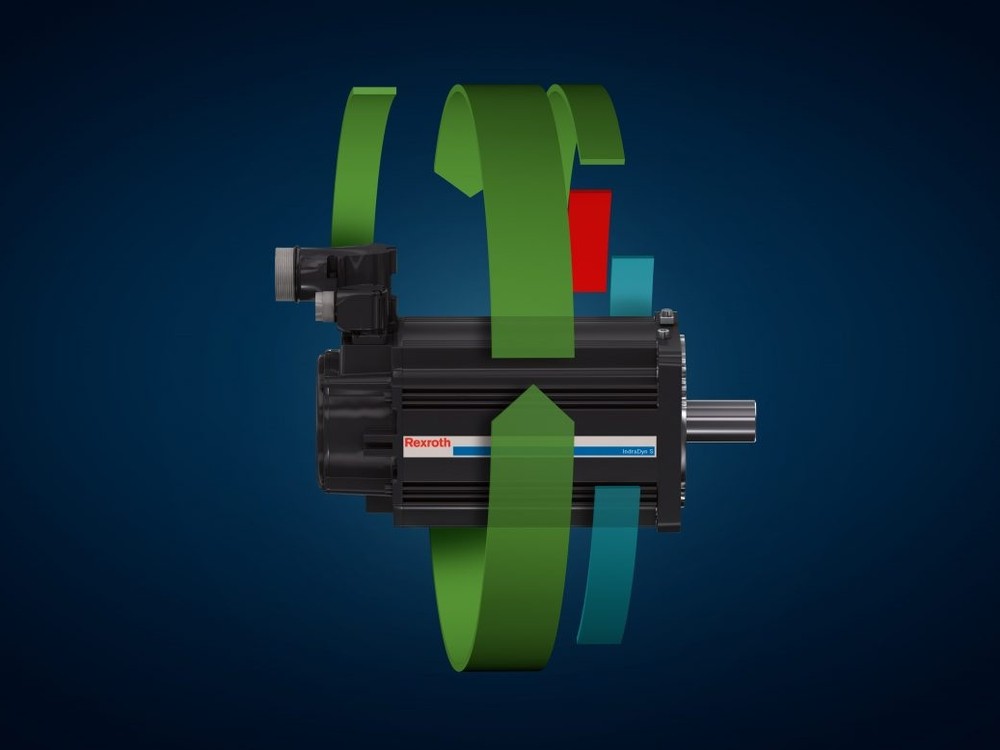
Refurbished products are becoming part of maintenance strategies, thanks to a more structured offer from automation manufacturers. The Geppia eye lifts the curtain on this new performance lever, both economic and environmental.
Repairing rather than replacing is a proposition that maintenance managers would like to take advantage of more often to reduce the environmental impact of industrial processes. However, they still face significant logistical and deadline constraints.
The pioneers of “circular maintenance” are, for the moment, mainly calling for the refurbishment of their own products (motors, variators, axes, etc.). A service which includes a systematic check of all components, preventive replacement of all wearing parts and software updates when necessary. At the end of this operation, the product is reinstated in its original machine with the same guarantees as if it were new.
The companies Guillin Emballages and Refresco, for example, explain in a white paper published by Bosch Rexroth that they regularly use refurbishment in addition to repair and retrofit, to respond to their obsolescence management issues.
Reconditioning could be a way for manufacturers to take the plunge into “circular maintenance” more quickly, by giving them access to products from other factories. Refurbished and reconditioned products indeed only have advantages. They help to guarantee the availability of production equipment in the face of lengthening parts supply times. They are significantly more economical than new products. And they help preserve essential non-renewable resources.
The implementation of large-scale take-back campaigns is a sign that the foundations for the development of reconditioned products are in place; the opportunity is just waiting to be seized