Neglecting its compressed air consumption is inflated!
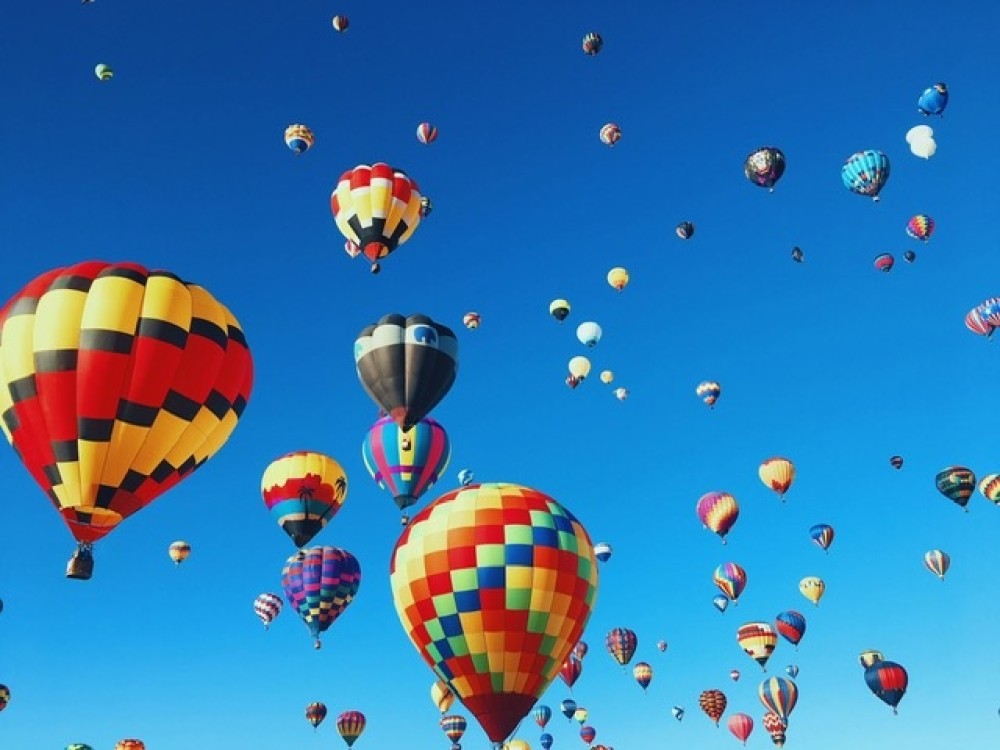
He regrets that compressed air is still too often at the bottom of the list of priorities, whereas it represents 20% of a plant’s consumption.
Air is considered a free resource. As a result, compressed air operates 24 hours a day, consumption is poorly monitored, components are often oversized and leaks numerous: this air that flies away is wasted energy, euros evaporating. Yet, just looking at it can quickly save money without having to mobilize a lot of resources. This can be several tens of thousands of euros per year for a small cooperative and several millions for global players with many production sites.” , he adds.
Cédric Lemoine also points to two other reasons why the subject of compressed air is neglected: the organization of purchases on the one hand, which does not value enough the economic benefits of components such as fittings, supplied as consumables; and, on the other hand, the lack of initial training in this field for technicians and engineers. “There are fewer and fewer experts in pneumatic engineering, which is a shame because there are many performance improvements to be made,” he says.
The pressure standard of industrial machines is now at 7 bars, whereas it would be perfectly possible to operate at 5 or even 4 bars. This is in any case the vision that Cédric Lemoine defends: if we play collectively, we can achieve this goal and reduce energy consumption related to compressed air by more than a third. I have already participated in machine evolution projects, in partnership with OEMs and end customers, for which we have achieved significant improvements. The next step, in my view, is to integrate compressor manufacturers into our work to redefine new energy-saving standards. Without them, there is a glass ceiling that we cannot climb.”
The main applications on which work can be done are, in order of importance, blowing (ejection, cleaning), pneumatic cylinders and vacuum gripping, which together account for 65% of compressed air consumption. «The blowing is by far the most energy-intensive job, it is an excellent candidate for a first optimization work as it is regularly reviewed from the point of view of hygienic safety» says Cédric Lemoine.
There are enough good practices and simple technical solutions to get the compressed air topic back on top, so will you make it your priority for the start of the new year?