Decontamination of packaging: technologies without chemicals make room for the sunDecontamination of packaging: technologies without chemicals make room for the sun
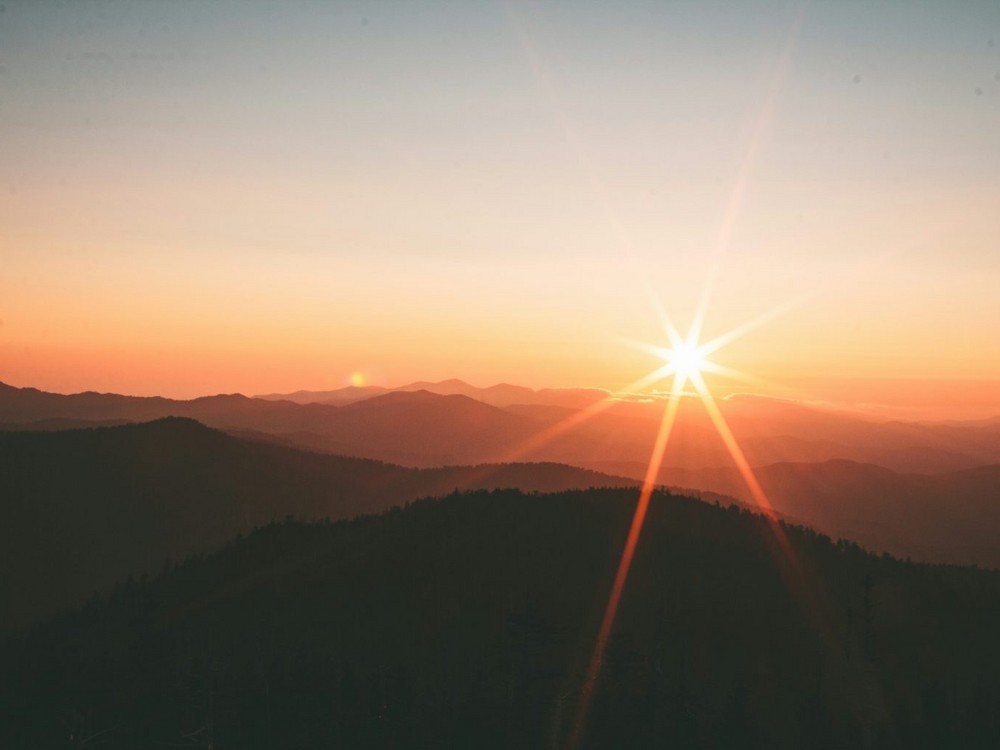
For Christophe Riedel, general manager of Claranor and pioneer of pulsed light, the motivations of industrialists are three orders: choosing a technology without chemistry is most often a matter of safety and working conditions. Then there are the economic and environmental reasons. The processes of decontamination by light are less energy-intensive. In addition, they do not generate effluents, which are beginning to be taxed in some countries.”
The various technologies on the market ensure all levels of decontamination, from the most basic to aseptic. Pulsed light is particularly well positioned on the intermediate levels: we generally respond to requests for ultra-clean packaging, which corresponds to hygiene class IV of the VDMA*. Products that require this level of hygiene are typically products that are not microbiologically stable, sold in a refrigerated circuit, have a pH greater than 4.6 or for which long DLC is desired. Milk and vegetable desserts, beverages such as kombucha are part of it. Ultra-clean packaging may also be required in the production of sauces, when products are either free of preservatives or pasteurized and then cold filled,” says Christophe Riedel.
For all these applications using light, the technical challenges are to be able to expose the entire surface of the package, for a sufficient time to kill microorganisms. The nature and form of packaging, as well as the production rate are criteria that will point to one technology rather than another, as is the level of decontamination expected. Overall, decontamination of films before packaging is formed is an application that works very well. The light is also used to obtain reductions of up to 3 logs on caps and collars of high-speed preforms, and more recently on pre-formed jars as well as metal cans.
One of the driving forces behind the adoption of chemical-free decontamination is the very positive feedback from experience, particularly the disappearance of contaminations after the installation of pulsed light equipment. These references are the most widely discussed within the groups and attest to the effectiveness of these systems. Then comes the industrial guarantee, namely the feedback of users who have operated equipment for long periods. Reliability and quality of customer service are crucial in this respect. We now have 15 years of experience on pulsed light globally, and this technology has been used for 10 years by Danone in the US. This is reassuring for all those who wish to get started,” concludes Christophe Riedel.
* Verband Deutscher Maschinen - und Anlagenbau; Association of German Machinery and Equipment Manufacturers