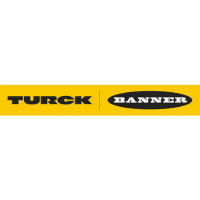
TURCK BANNER: Producer of components & solutions for automation. High quality product ranges offering innovative solutions!
Your partner in global automation
TURCK BANNER is a joint venture subsidiary of Hans Turck GmbH & Co. KG and Banner Engineering Corp. Turck, originating from Germany, specializes in manufacturing sensors, interfaces, and fieldbuses for industrial control and automation. Banner, from the USA, specializes in optoelectronic and ultrasonic sensors, safety components, and inspection systems.
For over 25 years, Turck and Banner have partnered to offer innovative solutions in industrial automation. Their expertise spans various industries, including automotive manufacturing, capital and consumer goods manufacturing, chemical and pharmaceutical industries, food industry, packaging and handling machines, and robotics.
TURCK BANNER is the exclusive representative for the French territory, responsible for sales operations, consulting and training activities, and technical support for Turck and Banner products. They market one of the widest ranges of automation components, utilizing state-of-the-art technologies that meet industrial environment standards or intrinsic safety requirements. Their sales organization covers all of France, directly engaging with industrial customers, machine manufacturers, users, or service providers, either directly or through a partner distribution network. The headquarters are located near Paris.
Facilities / Services TURCK BANNER
Turck Banner is a global partner for factory, process, and logistics automation across many industries. With their connected digital automation solutions, they are pioneers of Industry 4.0 and IIoT. As specialists in decentralized automation technology and smart sensors, Turck Banner brings intelligence to machines and ensures reliable detection, transmission, and processing of production data from sensors to the cloud. This is achieved not only with robust I/O solutions in IP67 but also with user-friendly software and services.
Their automation solutions increase the availability and efficiency of machines and plants in various industries and applications, from food, pharmaceuticals, and chemicals to automotive, mobile machines, intralogistics, and packaging. The knowledge of industry-specific applications, gained through intensive exchange with customers, combined with the development and production of electronics at the highest level, provides optimal solutions for customers' automation tasks.
With more than 5,000 employees worldwide developing, producing, and selling products and solutions in the areas of sensors, fieldbuses, control, cloud, connection, interface technologies, HMI, and RFID, Turck Banner maintains a global production and sales network, including over 30 subsidiaries and agencies in another 60 countries. Modern production facilities in Germany, Switzerland, Poland, the USA, Mexico, and China enable them to be flexible and respond quickly to local market requirements at any time.
Discover their latest Industry 4.0 concepts below...
Sensor to Cloud
Digitization is increasingly permeating industrial sectors. Technologies such as IO-Link, RFID, and Ethernet are increasing the amount of data from the machine environment, and cloud services enable mobile access worldwide. But how does one extract the relevant information from IoT without overloading networks or compromising protected content?
There are different ways and architectures for data retrieval. The first step is to generate this data. For that, Turck Banner proposes one of the broadest offerings of IO-Link sensors on the market.
Their remote I/Os can pre-process this data simply and efficiently, facilitated by their unique "ARGEE" technology. Their intelligent and programmable I/O modules with CODESYS are designed for integration into open and secure architectures. Their entire offering is equipped with multi-protocol technology allowing parallel data access.
For example, a PLC can communicate with their modules in PROFINET while the latter communicates in Modbus TCP with another device.
Their field devices serve as true IoT gateways, perfectly designed to interface with the cloud solution of choice. They offer both easily implementable cloud solutions dedicated to machine manufacturers and solutions oriented for end-users.
Condition Monitoring
The term "Condition Monitoring" refers to the process of monitoring a condition parameter in machines and systems. Nowadays, monitoring motors, electronic devices, or areas of a system for faults extends far beyond on-site inspections by workers.
Whether it's on ventilation systems, pumps, or motors of various sizes installed in production plants and warehouses, often in remote locations, machine maintenance can be time-consuming and error-prone, especially with rare on-site inspections.
Predictive maintenance and monitoring solutions allow customers to intervene on a machine when planned, not when a breakdown occurs in the middle of production.
Turck Banner solutions can be integrated as original equipment on newly designed machines or retrofitted on existing plants. Thanks to state-of-the-art sensor technology, intelligent field devices, and wireless transmission, condition monitoring can be continuous and remote. Systems can indicate impending failure early based on collected data. Reliable condition monitoring is essential for predictive maintenance.
Decentralized Automation
Efficiently automated machines and plants reduce costs, preserve product quality, and ensure high production availability. Breaking down rigid hierarchies and transferring responsibility to local components streamlines commissioning, reduces time-to-market, and simplifies resource expansion or relocation. Modularizing plants and machines offers new production freedoms.
Turck Banner is a recognized specialist in IP67 decentralization. Their sensors, I/O blocks, HMI, PLCs, power supplies, switches, connectors, lighting, and signaling enable conceiving modular machines without electrical boxes, reducing design, wiring, and startup times.
Agility in production is increasingly essential.
Decentralizing equipment and architecture allows machines to evolve quickly to adapt to production needs.
RFID identification, machine security, and condition monitoring are all independent components easily decentralized.
They can collaborate to study specific subjects or assist in designing machines according to a complete, flexible, and agile architecture.
Track & Trace (RFID)
End-to-end tracking of incoming and outgoing goods, automatically confirming the use of intended materials and tools in production or providing access points with increased security, requires powerful automatic identification technology. RFID has proven itself in Industry 4.0 with contactless transmission of large amounts of information, easy connection to higher-level systems, and long-distance communication.
HF (13.56 MHz) technology drives digital production processes, based on magnetic near-field communication. For longer ranges or mass readings of 200 or more data carriers, UHF technology (865...928 MHz) is preferred. Turck Banner's modular RFID system "BL ident" allows parallel operation of read/write heads in both HF and UHF ranges, directly on-site at the machine or plant, thanks to its IP67 protection rating, enabling decentralized signal processing.
Communication in logistics and production plants is hierarchical. RFID readers with Ethernet interfaces enable direct information exchange with higher-level systems such as PLCs, SCADA, MES, ERP, or the cloud, ensuring real-time visibility of goods movements, database matching, or automatic invoice generation.
The platform-independent OPC UA communication standard simplifies RFID solution integration into PLC, MES, ERP, or cloud systems. Turck has played a significant role in developing the standard and offers its RFID interface to the OPC UA server. Mixed operation of HF and UHF read/write heads ensures secure communication.
System integrators master parameterization of read/write heads and middleware installation, making information usable on data carriers by filtering, transmitting, or visualizing it as required.
Since 2018, Turck offers complete turnkey RFID solutions through its subsidiary, Turck Vilant Systems, increasing the efficiency of tracking and tracing processes along the supply chain.
Visual Factory
The factory of tomorrow communicates exchanges between machines or towards the ERP, but what about communication with operators or field maintenance agents?
Turck Banner offers programmable RGB lighting and signage solutions for visual communication in the field, aligning with Industry 4.0 demands. Simple machine status indicators become comprehensive, indicating heating time or starting cycles with rotating animations on luminous columns.
Operators are guided by lights, facilitating installation, assembly, or specific tasks. Machine areas illuminated in white can switch to red in case of stoppages, aiding maintenance personnel.
Manufacturing processes are visually displayed with clear indications. Tool or material changes are represented with specific color codes.
Tank levels are displayed with LED light bars resembling bar graphs. Communication with Turck Banner's lighting and indicators offers various options: IO LINK, MODBUS, SIO, PRO PULSE, adapting to customer architectures.
Turck Banner solutions give a voice to machines.
https://www.geppia.com/en/equipment-and-services/partners-suppliers/components-and-systems/industrial-connectivity-wiring-networks/turck-banner#sigProId18ab6c6bac